A hydraulic torque wrench is a highly professional hydraulic measuring instrument used to fasten and disassemble fasteners such as screws, bolts, nuts, etc. It has a thin thickness, especially suitable for places where space is relatively small. The hydraulic torque wrench utilizes a controllable applied torque to ensure that the fastener will not damage the thread due to excessive torque.
Specification
Model |
T-2NJZK |
T-3NJZK |
T-4NJZK |
T-8NJZK |
Torque (Nm) |
237-2370 |
345-3446 |
546-5458 |
1055-10550 |
Nut Range (S) |
36-55 |
36-60 |
46-80 |
70-105 |
Power Unit Weight (kg) |
0.8 |
0.8 |
1.9 |
4.2 |
Work Unit Weight (kg) |
1.5 |
1.7 |
3.6 |
7.6 |
L |
192 |
218 |
266 |
324 |
H1 |
105 |
118 |
139 |
171 |
H2 |
147 |
156 |
167 |
198 |
W1 |
32 |
32 |
42 |
53 |
W2 |
50 |
50 |
66 |
83 |
Hydraulic Torque Wrench Figure
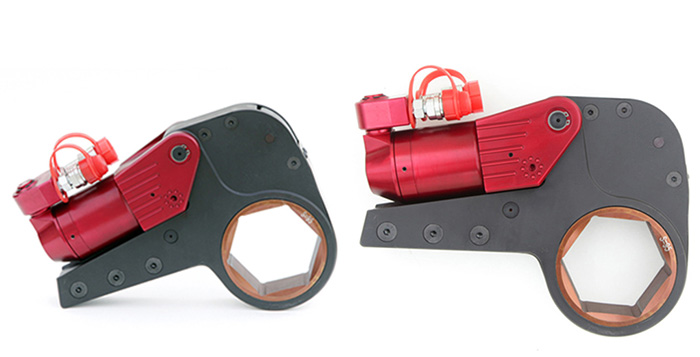
Features
A hydraulic torque wrench is a tool used to apply a specific amount of torque to a bolt or nut. It is powered by hydraulic pressure and is typically used in heavy-duty applications such as construction, oil and gas, and mining industries. Some common features of a hydraulic torque wrench include:
- High torque output: Hydraulic torque wrenches can generate very high levels of torque, making them ideal for heavy-duty applications where a lot of force is required.
- Precise torque control: Hydraulic torque wrenches can apply torque with a high degree of accuracy, ensuring that the correct amount of torque is applied to the bolt or nut.
- Lightweight and compact: Hydraulic torque wrenches are typically smaller and lighter than other types of torque wrenches, making them easier to handle and maneuver in tight spaces.
- Easy to operate: Hydraulic torque wrenches are relatively simple to operate and require minimal training to use effectively.
- Durability: Hydraulic torque wrenches are designed to withstand the rigors of heavy-duty use and are typically built from high-quality materials that can withstand a lot of wear and tear.
- Safety features: Many hydraulic torque wrenches come with safety features such as overload protection, which prevents the tool from applying too much torque and causing damage to the bolt or nut.
Application
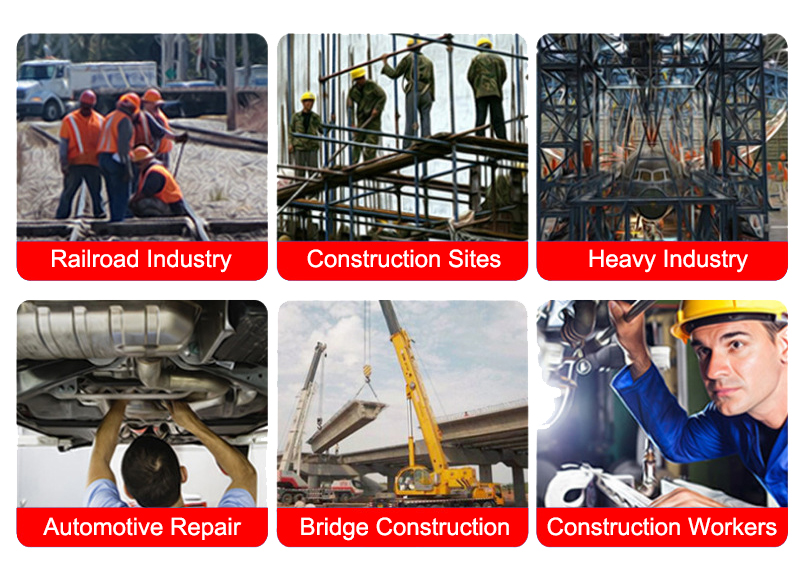
Hydraulic torque wrenches are commonly used in a variety of applications that require high levels of torque and precision. Some common applications of hydraulic torque wrenches include:
- Industrial machinery: Hydraulic torque wrenches are used to tighten bolts and nuts on large industrial machines, such as turbines, generators, and pumps.
- Oil and gas industry: Hydraulic torque wrenches are used in the oil and gas industry to tighten bolts and nuts on pipelines, valves, and other equipment.
- Construction industry: Hydraulic torque wrenches are used in construction to tighten bolts and nuts on steel structures, bridges, and other infrastructure projects.
- Mining industry: Hydraulic torque wrenches are used in the mining industry to tighten bolts and nuts on heavy machineries such as excavators, bulldozers, and drilling rigs.
- Wind energy industry: Hydraulic torque wrenches are used in the wind energy industry to tighten bolts and nuts on wind turbines, which require high levels of torque to maintain stability in high winds.
- Aerospace industry: Hydraulic torque wrenches are used in the aerospace industry to tighten bolts and nuts on aircraft engines, landing gear, and other components.
Overall, hydraulic torque wrenches are essential tools in a variety of heavy-duty applications where accuracy, precision, and high torque output are critical for successful operation.
Tips: How to maintain a hydraulic torque wrench?
Hydraulic torque wrenches are powerful tools that are commonly used in various industries for tightening and loosening bolts and nuts. Proper maintenance of these tools is essential to ensure their optimal performance and longevity. Here are some tips on how to maintain a hydraulic torque wrench:
- Keep the wrench clean: After each use, wipe the wrench with a clean cloth to remove any debris or dirt that may have accumulated on it. This will prevent the build-up of grime that can damage the tool.
- Regularly check the hydraulic oil level: Hydraulic torque wrenches operate using hydraulic fluid. Check the fluid level in the reservoir regularly, and top it up as needed. Ensure that the hydraulic oil used is of the correct type and grade.
- Inspect the hoses: Check the hydraulic hoses for any signs of wear or damage. Replace any damaged hoses immediately to prevent leaks and possible accidents.
- Check the tool's fittings and seals: Regularly inspect the wrench's fittings and seals for any signs of wear or damage. Replace any worn or damaged fittings and seals to prevent leaks and ensure the tool's proper functioning.
- Lubricate the moving parts: Lubricate the moving parts of the wrench regularly with a suitable lubricant to prevent corrosion and ensure smooth operation.
- Store the wrench properly: Store the wrench in a clean and dry place, free from any moisture, dust, or debris. Use the appropriate protective covers to prevent damage to the tool during storage.
- By following these tips, you can ensure that your hydraulic torque wrench is well-maintained, and will continue to perform at its best for many years to come.
FAQs of the hydraulic torque wrench
- How does a hydraulic torque wrench work?
A hydraulic torque wrench uses a hydraulic cylinder to generate high levels of torque that are then transmitted to the bolt or nut. The hydraulic pressure is controlled by a pump, and the tool is operated by a control valve.
- What types of applications are hydraulic torque wrenches used for?
Hydraulic torque wrenches are commonly used in various industries, including construction, manufacturing, oil and gas, and mining. They are used for applications such as pipeline construction, machinery assembly, and heavy equipment maintenance.
- How do I choose the right hydraulic torque wrench for my application?
Choosing the right hydraulic torque wrench depends on several factors, including the bolt size, the required torque output, and the working conditions. Consulting with a torque tool specialist or a manufacturer can help ensure that you choose the right tool for your application.